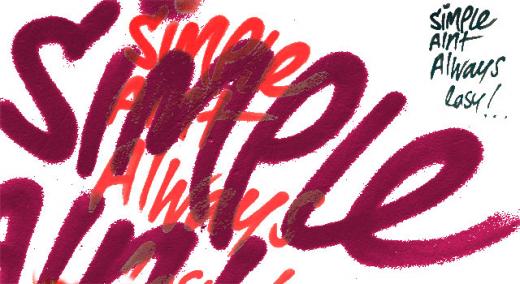
Adapted from "Simple Ain't Always Easy." Credit: duncan c
The “mantra” for continuous improvement is to learn from our mistakes. Not only learn but also take necessary actions and come up with strategies to prevent the recurrence of the same or similar mistakes. It is true for humans as well as for businesses. In business, especially in the oil and gas industry—due to engineering and installation complexities, vast supply chains, and high quality and safety risks—the lessons-learned (LL) program is a key part of the quality management system (QMS) and continuous improvement efforts.
ADVERTISEMENT |
Often, companies in the oil and gas industry have LL programs (systems and processes) in place. However, despite having LL programs, why are the same or similar mistakes are still being repeated. Why is this? Here are 10 key concepts that companies in the oil and gas industry and the personnel designing LL programs should bear in mind to ensure LL programs add value and are efficient, effective, and successful.
…
Add new comment