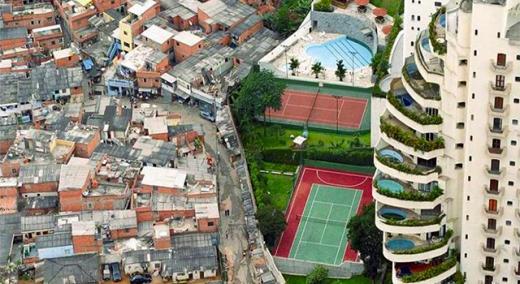
Most of us have learned that being busy does not mean you’re being productive, and that multitasking leads to being less productive—although I still see that being harped on as a “skill” on resumes and profiles. Leading organizations manage by clearly defined objectives rather than arbitrary and often unrelated work hours, enabling flexible workplaces that create additional value for everyone.
ADVERTISEMENT |
With that said, we still like deadlines and other time constraints. Used properly, they enable progress and force decisions. Used improperly and arbitrarily, perhaps more common than not, they create chaos, stress, lower quality, and poor decision making. Where’s the balance? We often say that a sign of a good leader is knowing when there is sufficient information to make a decision—not too little and not waiting for too much. Under the stress inherent in most organizations, this often skews toward too little.
…
Add new comment