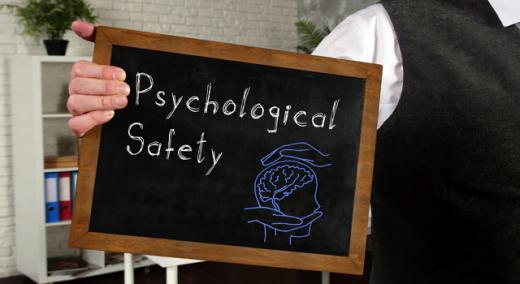
I can’t count how many times during the past 20 years I’ve heard executives complain that their people aren’t enthusiastically participating in their lean program. Leaders lament that while the company has spent a small fortune to put everybody through continuous improvement training, hardly anybody submits ideas. The problem isn’t their employees; it’s a cultural problem and, therefore, a leadership problem.
ADVERTISEMENT |
These frustrated leaders often try to force employees to participate through incentives and quotas. A better strategy for leaders is taking responsibility and working to reduce two key cultural factors that keep employees from speaking up: fear and futility.
In an environment of fear and punishment, employees understandably protect themselves by staying quiet about opportunities for improvement, which comes at a great cost to the organization. How do we address this? Don’t just tell employees they should feel safe or be brave in the face of fear. Eliminating fear is crucial, as W. Edwards Deming said decades ago. We need to replace fear with psychological safety.
…
Comments
Check out my new book
For a deeper dive into these themes of psychological safety and problem solving, please check out my latest book, "The Mistakes That Make Us: Cultivating a Culture of Learning and Innovation" -- https://mistakesbook.com/
Getting Problem Solving to work
Hi,
The problem of expensive training in problem solving (and Lean Six sigma) being imparted but not used suggested by you is very real.
However the solution is recognised explicitly and very comprehensively dealt in the Japanese TQM where the 3 componenets included in any training are - JIT (lean), TQC (Six Sigma) and Total Employee Invovlvement (TEI). It is emphasised that without TEI there is no improevment because intitating change involves risk. The barriers to Employee Involvement (i.e. factors that even cause exclusion) and ways to overcome them are included in the training formally.
Regards,
Niraj
Well Said
Thanks for a good article.
I'd ad one more element of safety: safe to try something and have it "fail"
If people are expected only to succeed every time they submit an improvement, they will avoid submitting ideas that might not work out.
Great point
Hi Jonathon - Yes, I agree. I tried to say as much in the article, but you stated it more clearly :-)
That's the need for Psychological Safety in the Study and Adjust phases of the PDSA cycle.
If leaders can't accept it when people try to improve and "fail" (fall short of desired improvement), then that will drive people to be very hesitant to try anything but the safest of improvements...
So True!
Dear Mark,
Your article is so resoundingly true. I am very fortunate to work for a HC facility that has a fully developed Organizational Development department that attempts to walk with leadership at their pace. With that said, we face major challenges where bandwidth is at 'war' with time allotment toward human development. While I don't believe this will get much better in the near future - if ever - I believe we can have small wins along the way and your words continue to encourage.
Thank-you for your motivating piece!
Add new comment