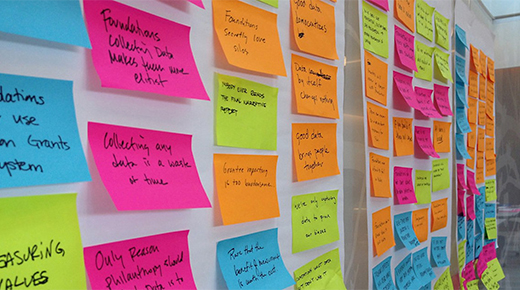
Dramatic cost savings. Lead time and inventory reductions. Improved transactional processes. Although lean has its roots in manufacturing, nearly every industry and type of organization around the world can benefit from it. A little while back, we reviewed the “Five Critical Lean Tools” that are a great way to get started implementing lean. Today, let’s continue with five more critical lean tools.
ADVERTISEMENT |
1. Kaizen
Kaizen is a method for accelerating process improvement projects. Although originally developed for manufacturing, kaizen is used extensively in a variety of industries and is a valuable technique for the process improvement practitioner. Kaizen is a focused three- to five-day dedicated event to drive process improvements. Employees are pulled from their daily duties to participate. Solutions are implemented immediately. Leaders can use Minitab’s Companion Roadmap to better plan and implement a kaizen event:
…
Add new comment