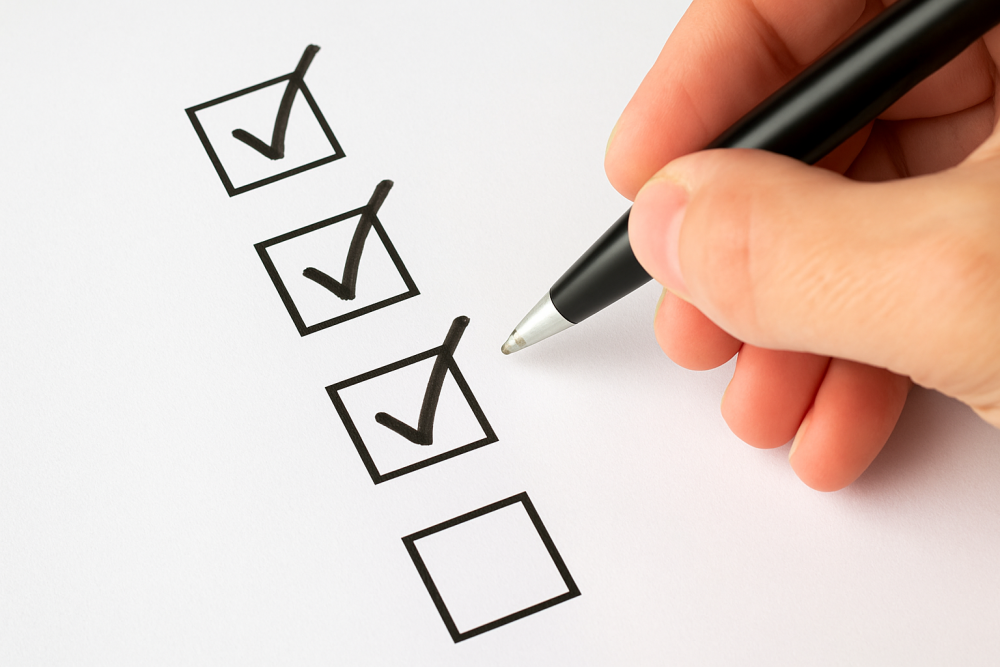
The six core questions you see below are a window to help us understand why we struggle at work. Why? Because the answers to them are missing! The remedy is to first notice that—to notice the motion caused by those deficits. Then remove the motion by implementing visual answers. Imbed the answers into the living landscape of work.
ADVERTISEMENT |
Here are examples that show you what I mean when I say: Make each core question visual. Just bear in mind that the six core questions are a tool, not a systematic methodology. They will move you closer to workplace visuality but can’t get you to the destination: a fully-functioning visual workplace.
|
…
Add new comment