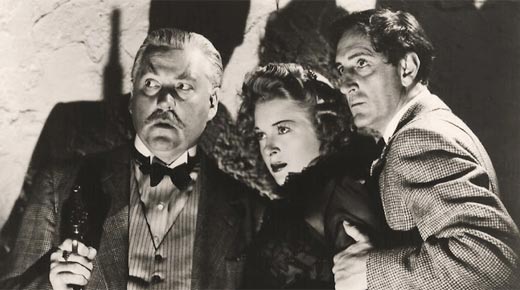
Although not a quality guru, the fictional detective Sherlock Holmes took a methodical approach to problem solving that can be useful when applied to root cause analysis (RCA) during the investigation of a product or process failure.
ADVERTISEMENT |
Sir Arthur Conan Doyle (1859–1930) was a British physician who created the character Sherlock Holmes. Doyle published 56 short stories and four novels between 1886–1893 and 1903–1927. In addition to Doyle’s original stories, countless authors, including Mark Twain, have also tried their hand at writing Sherlock Holmes stories, and the detective has featured in radio serials, films, and video games.
While enjoying Sherlock Holmes’ adventures, quality professionals can pick up tips for performing root cause analysis. Here are a few from several of Doyle’s stories.
The Copper Beeches
“‘Data! data! data!’ he cried impatiently. ‘I can’t make bricks without clay.’”
…
Comments
Excellent
I have not lived for years with Sherlock Holmes for nothing.
Dr. John Watson
-The Hounds of the Baskervilles
Add new comment