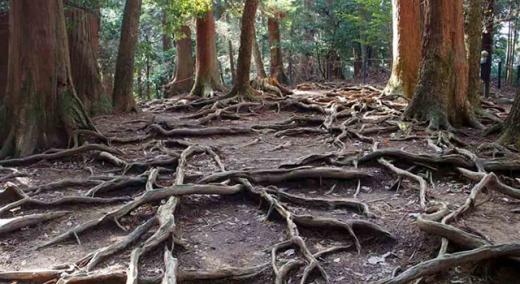
In a recent article I discussed the traditional 5S audit, shared a set of reservations, and offered some remedies—“The Five Tweaks,” as I called them. Remedies are important because most of you have a vested interest in continuing regular audits but want them to be successful and more valued. The five tweaks should help.
ADVERTISEMENT |
Do you want to go still further so your audit begins to assess outcomes that are more worthy of praise and therefore of the steady, sustained attention of your associates? If so, pursue Tweak No. 1: Audit for Principles. This means auditing for the extent to which 5S principles are in place, not whether 5S tasks are done. Do that, and your monthly audit will begin to become an improvement driver, instead of a mere compliance tool. Here’s an example.
S2: Shine
In the logic of a traditional 5S audit, S2: Shine supports as an outcome a clean work area... and everything in it. And we all know that can and will happen over time, given steady, applied effort and some decent cleaning supplies. Here’s what that audit item usually reads like in two examples that differ only in scoring styles:
…
Add new comment