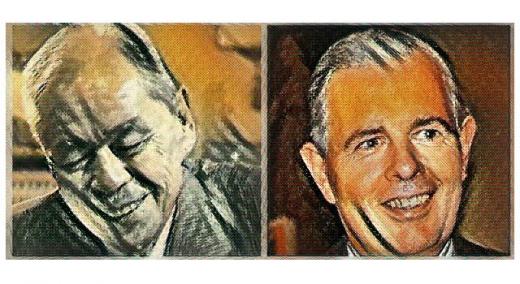
One of my favorite equations from Factory Physics, by Wallace Hopp and Mark Spearman (Waveland Press, third edition, 2011) is Kingman’s formula, usually represented as “VUT.”
ADVERTISEMENT |
The VUT equation is named after Sir John Kingman, a British mathematician:
The first factor represents variability and is a combination of variability factors representing arrival and service times (e.g., flow variability and process variability). The second factor represents utilization of the workstation or the assembly line. The third factor represents the average processing time in the workstation or the assembly line. The VUT equation shows that the average cycle time or wait time is proportional to the product of variability, utilization, and process time.
The most important lesson from VUT is: If a station increases utilization without making any other change, average work in process (WIP) and cycle time will increase in a highly nonlinear fashion.
…
Comments
Variation impacts production management
This article is extremely important from not only a quality but also an operations management perspective. Goldratt's and Cox's The Goal showed why, in a balanced factory without excess capacity (or even if there is some excess capacity), favorable variation in processing and material transfer times does not offset unfavorable variation, with the result that inventory piles up.
A good takeaway from this article is that we need to think about variation in processing and material transfer times (service and arrival times in the VUT equation shown here) as well as variation in part dimensions, which is what quality practitioners usually think about when variation is mentioned. I never thought of the kind of variation mentioned in this article until I read The Goal, in a factory that was implementing Goldratt's methods.
Add new comment