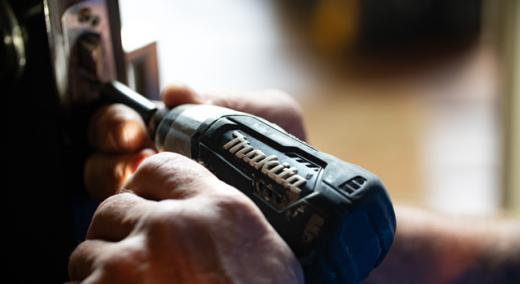
Benjamin Franklin said, “... in this world nothing can be said to be certain, except death and taxes.” If you work in maintenance, you know that equipment failure is also on that list.
ADVERTISEMENT |
As inevitable as equipment failures are, by paying close attention to mean time to recovery (MTTR), you can make sure failures and outages are resolved efficiently with the smallest possible affect on your organization’s bottom line.
In this article you’ll learn what MTTR is, why it’s important, and how to calculate and—most important—reduce it.
Mean time incident metrics overview
Managing system failure well means minimizing its negative effect. To help you effectively manage losses, several critical metrics should be monitored.
What are the key metrics your maintenance data can give you?
• MTTR (mean time to repair)
• MTBF (mean time between failures)
• MTTF (mean time to failure)
…
Add new comment