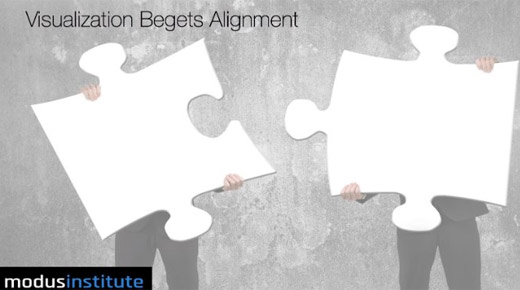
Lean says: Map the value stream. Your brain says: I’ve been doing this so long, it’s become second nature to me. The steps are right here—in my head.
ADVERTISEMENT |
What’s at play here:
• Illusion of transparency
• Curse of knowledge/information imbalance
• Status quo thinking
• Groupthink/false consensus effect
• Availability bias
It was day four of the value-stream mapping exercise, and tempers were beginning to fray. Despite having worked together for years, the members of this outwardly cohesive development team struggled to identify the basic activities needed to create value for their customer. While at 17 steps they agreed they were close to completing a first pass of their map, they couldn’t seem to reach consensus when it came to certain conditions and boundaries, and for some, even the target was nebulous.
If they couldn’t agree on how they currently operate—without that clear baseline—how could they improve their future state?
…
Add new comment