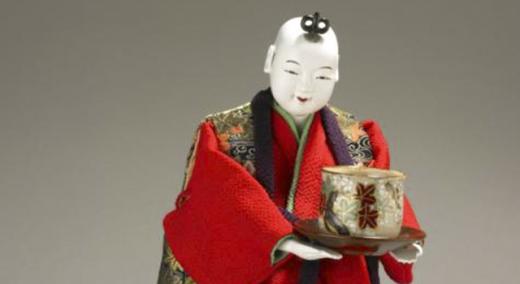
As readers of my columns know, I am an ardent student of the Toyota Production System (TPS). One of the core philosophies of TPS is kaizen, often translated from Japanese as “continuous improvement.” It is the idea that one should continuously find ways to eliminate nonvalue-adding activities, and in the process develop oneself and others to get better at kaizen. The idea of kaizen begetting more kaizen.
ADVERTISEMENT |
Kaizen is a human capital enrichment philosophy. As Eiji Toyoda, Toyota Motor Corp.’s president from 1967 to 1982, said, “It is people that make things, and so people must be developed before work can start.”
…
Add new comment