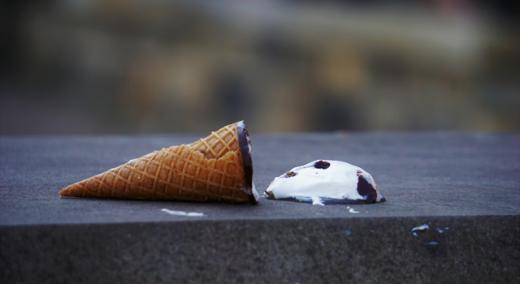
We all make mistakes. Despite a vigorous editing process, there may even be one in this article! Although everyone makes mistakes, not everyone owns up to them, and thus they miss an opportunity to grow, learn, and—if they appreciate and apply what they’ve learned—consistently improve the quality of their work.
ADVERTISEMENT |
That’s the entire idea behind kaizen, or the concept of continuous improvement, which we often talk about here at Quality Digest. Ongoing improvement means many things: adjusting, eliminating waste, finding inefficiencies, and building a better process. But one aspect that often gets ignored is that very niche subject of mistakes. More specifically, how do we predict, find, correct, and avoid them to foster consistent improvement? And who better to talk to about that process of efficiency and growth in the workplace than Mark Graban?
…
Comments
Thanks, Megan!
Megan, thanks for interviewing me and for this great write-up and summary at the end.
Absolutely my pleasure, Mark!
Add new comment