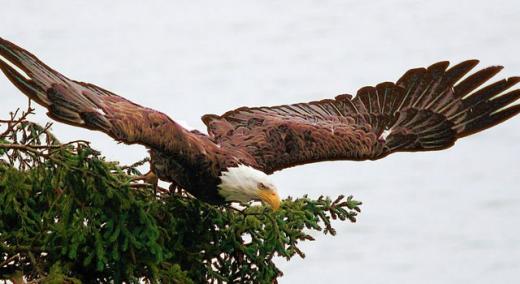
Most people have a notion about the visual workplace that is much too small for themselves and their companies. They think of it as a series of point solutions that are helpful, even clever. Yet they should expect more—because they need more.
ADVERTISEMENT |
In fact, visuality is a language—an imbedded system of information detail. Its purpose (among many other things) is to capture and make functional the elements of your current operational system. This is as true in healthcare and offices as it is in manufacturing, food processing, or an open-pit mine. On its most effective level, the visual workplace allows you and your company to see how you think—and where the gaps are. I call these gaps “information deficits” and they are barely visible on their own. To find them we must look for their symptom: motion/moving without working.
Visual devices and systems are the words and grammar of your new imbedded language. The result is a workplace that speaks—whatever the venue—along with dramatic increases in productivity quality, safety, and the satisfaction of employees and customers alike.
…
Add new comment