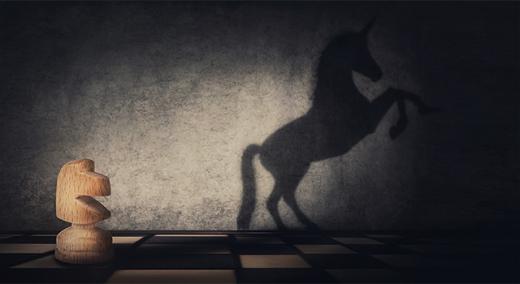
The quality profession has been evolving since the Industrial Revolution. I’ve lived part of this journey since the 1970s and have experienced its effect. ASQ and other organizations have continually pushed the envelope in creating training and certifications in the skill sets we’ve developed over the decades. These initiatives have facilitated an improvement in overall defect levels combined with a steady decline in organizational risk. Unfortunately, the positive trends appear to have flattened during the last decade.
ADVERTISEMENT |
As the timeline below depicts, we’ve successfully matured by creating conformance and performance tools. In my experience, however, we’ve never had a unified mandate to evolve beyond conformance to business excellence. Regrettably, we’ve reached a virtual event horizon that could be correlated with the Covid-19 pandemic.
…
Comments
Excellent
I'm really looking forward to this series. As ever, I believe your diagnosis and prognosis for the profession is bang on the mark. I have been selling myself as something more akin to a business consultant than anything connected to 'traditional' quality for some time now.
My only quibble may be with your lead-in to the 'risk' article. Complete risk avoidance isn't always healthy. I work for a business that does very nicely indeed as a result of embracing significant product risks.
Add new comment