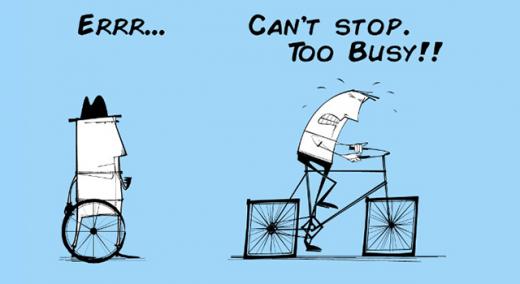
Lean manufacturing is a philosophy focused on maximizing productivity and eliminating waste while creating a quality product. One of the most powerful strategies in the lean toolbox is total productive maintenance (TPM), a system targeting continuous improvement through a holistic approach to maintenance. Avoid delays in the manufacturing process caused by breakdowns and unplanned maintenance with TPM.
ADVERTISEMENT |
What is total productive maintenance?
As long as equipment and tools have been used, they’ve needed to be maintained. In manufacturing, maintenance traditionally was approached reactively, and as Steven Borris writes in Total Productive Maintenance (McGraw Hill Education, 2006), traditionally the surplus of cheap labor meant no one was particularly worried about efficiency or avoiding breakdowns. Following World War II, however, industries and economies were reassessing business and making drastic changes.
…
Add new comment