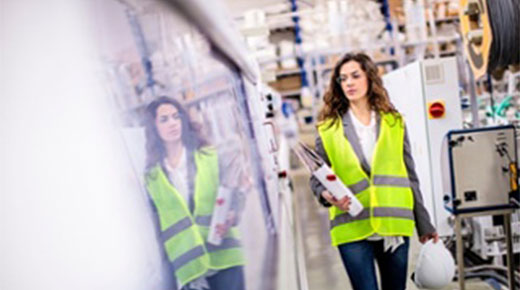
Reading the Automotive Industry Action Group’s CQI-8 Layered Process Audit (LPA) Guideline, you might notice a line saying LPAs are “completed on site ‘where the work is done.’”
ADVERTISEMENT |
For lean manufacturing experts, this specific quote might bring to mind gemba walks, a method where leaders observe and solve problems on the shop floor. In Japanese, gemba means “the real place,” or in manufacturing, where the work is done.
Whether the reference is intentional or not, LPAs and gemba walks share clear similarities. Could this be why companies doing gemba walks have an easier time with LPA programs, despite their complexity? This article compares gemba walks with LPAs, exploring how to tell if you’re ready for LPAs and how to prepare.
…
Comments
step up or step down?
I have no doubt that Mr. Whitworth believes there is value in making the required LPA approach as useful as possible. The subheading of the article is probably accurate: Mr. Wentowrth's approach to the LPA is no doubt a natural progression of internal auditing. And I'm sure that his firm's checklists and approaches will help you provide solid objective evidence that the audits were done and more importantly the objective evidence will be in a form that any auditor will readily recognize and accept. I don't mean to denigrate Mr. Wentworth's work in any way. Raer, I am questioning the questioning the basic premise that the 'objective evidence' approach of most of our 'management system standards' makes anything better. It makes the auditor adn the audit host's job a lot easier, but it doesn't improve business.
The LPA will not provide you with the value that a true gemba walk culture will provide you. The gaps between a real gemba walk and a 'formal audit' process are not trivial. In my experience we are moving backwards (away from Lean and the Toyota Production System) when we go from gemba walks to any formalized 'audit' process.
The real downside of the LPA is the same as any method required or suggested by any management system standard: the obssession with 'objective evidence' that something happened as planned. This is all waste. The paper work becomes more important than the actual effectiveness of the walk. It also tends to result in far fewer 'walks' than when the walks are done because the manager knows first hand how useful they are. When true gemba walks are being done the 'objective evidence' is seen in the continual improvement of the key metrics of quality, delivery, delivery, cost and employeee engagement. If you as a senior leader are not sure if the gemba walks are being done and done properly, go on your own gemba walks - you don't need a report.
Mr. Wentworth is correct: the hard work begins with the findings. Regardless of whether the findings come from a true gemba walk or a formal audit. So why not just skip the paperwork and concentrate on the waste?
Add new comment