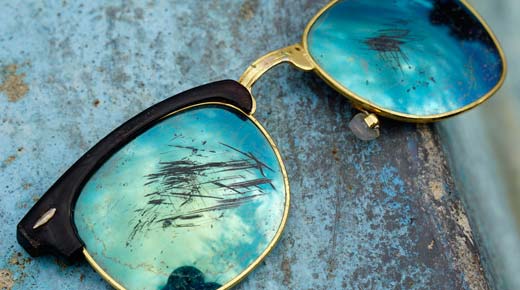
Scratches: Product failure or process failure?
Credit: Stef
Body
To meet the 2018 deadline for becoming certified to ISO 9001:2015, organizations are scrambling to overhaul their quality management systems. One major revision to ISO 9001 is the requirement to identify, evaluate, and address risks. Unfortunately, a tool most appropriate for these actions has fallen to the wayside. Failure mode and effects analysis (FMEA) is the perfect tool to satisfy an organization’s risk analysis needs—provided that the technique is understood.
…
Want to continue?
Log in or create a FREE account.
By logging in you agree to receive communication from Quality Digest.
Privacy Policy.
Comments
The Old Forms Are Fine When Used Correctly
I have taught and implemented FMEAs for over 30 years. I have applied them to well over a thousand products from a wide variety of industries. I have seen their proper use improve the design and manufacture of a wide variety of products including molecular assays for the detection of various diseases including HIV, late stage cancer treatments, hybrid vehicles, flat screen TVs and just about every automotive component you can think of. Standard AIAG Design and Process forms were used that included a class column. Let me begin by saying that the forms are fine, it is what we are putting in the forms that is the problem. If you know what goes in each column and properly calculate and use the Class Column to determine the issues you must work on instead of RPN, you will be well on your way to improving your products and processes.
The paper spends considerable time talking about an FMEA. There is no such thing as an “FMEA”. There are multiple types of FMEAs all with very different purposes. Design FMEAs are used to manage risk due to the design’s current design specifications. Improper design specifications are one of the major sources of risk that companies who design products face.
The Process FMEA is used to manage risk due to the current process. There are many sources of risks that Process FMEAs can be used to manage. Most Process FMEAs are done on manufacturing processes due to the demands of industry for their use. Exposure to harm occurs in these processes when an out of spec condition such as scratches is created by the process.
Process FMEAs can be used to manage risk due to non-manufacturing processes as well. Any time a process fails to create a desired output or creates an undesirable output, exposure to harm occurs.
Machinery FMEAs, when used correctly (99.9% are not), is an excellent to tool for managing risk due to improper manufacturing process design. Since the focus of the Machinery FMEA is the design of a process, the majority of people create a Machinery FMEA that looks more like a Process FMEA which negates the value of the tool.
The following example is provided by the author as an improper FMEA:
Potential failure mode: Part scratched Potential effect(s) of failure: Customer rejects part Severity: 5 Cause(s)/mechanism(s) of failure: Operator did not detect the scratch Recommended actions: None (because the occurrence was rated at 5 and detections at a 4, which makes the total risk priority number = 100). Typically, organizations do not apply a risk treatment to RPN values at or under 100.
Contrary to what the article states, the problem with the example is not the ”Part Scratched” failure mode. This is actually a legitimate failure mode assuming scratches are an out of spec condition. The three major problems with the example is the cause listed and the fact that the author left out two critical columns of the Process FMEA. “Operator did not detect the scratch” is not a failure cause. There are 10 different types of root causes that all processes should be examined for. One of those is mishandling of parts. In the example provided by the author, operators can create scratches by stacking parts on the conveyor. Consequently, our failure cause is “Operator stacks parts on conveyor”. The proper definition of the root causes of process failure is the most important step of the Process FMEA process since it allows us to define the required “Prevention Controls”. The Prevention control column describes how the failure causes (sources of incidents that lead to exposure to harm) will be prevented. This column contains the primary risk controls for the process.
The next step is to fill out the “Prevention Controls” column. When the Failure Cause column is properly filled out, the majority of the required Prevention Controls become obvious. One simply must ask what control must be implemented to prevent the cause. In the example provided, one may decide to implement procedures on product handling. While implementing Process FMEAs as a Plant Manager for Ford Motor Company which resulted in average weekly cost savings of $144,000 after nine months of implementation, we implemented over 15,000 controls many of which were simple and cost very little money.
The last column that must be filled out that the author left out of the paper is the “Detection Controls” column. This column is used to capture the checks that will be made to contain unacceptable process outputs or failure modes. In a properly constructed Process FMEA your Prevention Controls often outnumber the quantity of Detection controls by a factor of 10 to 1.
The author proposes the following as a proper FMEA:
Potential failure mode/Potential process function failure: Operators are unable to utilize a one-piece flow to package parts Potential effect(s) of failure/Potential effects of the process function failure: Parts are removed and stacked on a table, which causes appearance defects such as scratches, scuffs, dents, and chips. Customer rejects Severity: 5 Cause(s)/mechanism(s) of failure/Root cause (why would the process function failure occur?): One-piece flow not designed into or utilized at the process work cell.
It is difficult to tell what kind of FMEA the author intends to do. If one were creating a Machinery FMEA, the requirement that the “Operator must be able to utilize a one-piece flow to package parts” would be a legitimate entry for the Requirements column of the Machinery FMEA. The failure mode and effects provided by the author would then be legitimate. The example falls apart at the cause entry. In a properly completed Machinery FMEA a detailed description of the equipment specified to accomplish the one-piece flow would be listed. A Design Controls column would also be included to define the methods used to ensure that the one-piece flow could be supported.
It is also surprising the Prevention and Detection Controls column are left out of the example of a "good" FMEA provided by the author. The Recommended Actions column is used to capture actions that will be attempted to reduce risk. In real life, some will be work and be implmented and some will not. This column is not intended to contain your risk prevention and mitigation controls. That is the job of the Prevention and Detection columns.
It is imporant to know how the various FMEA types are used to manage risk. As an example, let us look at the Process FMEA. The Failure Mode Column of the Process FMEA is the objectionable incident that leads to exposure to harm. The Effects Column contains a description of the harm. The Severity Column is a measure of the level of harm. The Failure Cause Column is the source of the objectionable incident. The Occurrence Column is a measure of the probability of the objectionable incident and subsequent exposure to harm due to the source capture in the Failure Cause column. The Class Column, determined from the Severity and Occurrence Columns defines the level of risk for the Process FMEA line being evaluated. It tells you what the lines that have objectionable risk and what must be worked on. The Prevention and Detection columns are used to capture the risk prevention and detection controls. The Recommended Actions area is used to capture actions that will be taken in an attempt to reduce risk. Some will be implemented and some will not. If implemented, the associated columns of the Process FMEA must be updated.
In closing, Machinery, Design and Process FMEAs are powerful examples of the “Risk Based Thinking” required by ISO 9001:2015 when understood and implemented correctly. New Machinery, Design and Process FMEA forms are not needed. Knowledge on how to properly use them is. Tremendous benefits are available to you when these tools are used correclty.
If you would like to learn more about FMEAs and/or how to use FMEAs to help you comply with ISO 9001:2015 visit www.harpcosystems.com or contact me at Richard.harpster@harpcosystems.com.
Please do not miss my point
Normally, I do not respond to any criticism posted from my articles because I figure everyone has their own opinion and can draw their own conclusions to the material I put out there for my readers to use. The articles I publish are not just an off the cuff topic that are created to just fill up space. I try to share some realistic real world conditions that I have experienced (actually being at the Gemba) so that others may avoid the same pitfalls. I love to see discussions break out where many “on-the-ground” Engineers share certain aspects of their experiences and make points that we can all learn from.
I certainly DO NOT comb the internet looking for articles published by my engineering colleagues so that I can nitpick every detail in order to promote my consulting business for free.
The example in the article of course was not in great detail and of course not all of the FMEA requirements were covered. Nor were the various types of FMEA’s as mentioned in the response by Richard. The point of the article was not to be an in-depth training manual for FMEA’s, merely a reminder that the FMEA is best used for risk assessment in the process and FROM MY EXPERIENCE (actually being at the Gemba) what I have seen the FMEA being used for. Every FMEA I have helped my suppliers with over the past 3 years has been improved by simply renaming the column headings so they flow much easier during the development. My point I realize will not be understood by everyone and that’s perfectly OK with me.
I would like to apologize to all my readers for drawing out such a comment that brings nothing to the discussion but an attempt to discredit my article and promote his own interest.
Before You Change Anything Make Sure It Is Required
Let me begin by saying that I “do not comb the internet looking for articles published by my engineering colleagues so that I can nitpick every detail in order to promote my consulting business for free”. I have spent the last 30 years of my life optimizing FMEAs and other related tools for the purpose of improving companies product and process development systems. Along with internal development activities, I am constantly doing reading from sources of all types to stay on top of any new advancements. Consequently, when I received an email from Quality Digest that an article titled “Same Old Routine With FMEA: Not With ISO 9001:2015” was available, I was very interested in reading it.
The changing of Process FMEA column headings has a significant impact on both the performance of the Process FMEA as well as other tools the Process FMEA must be integrated with in an effective Risk Based Product Lifecycle Management system. Consequently, one must make sure the changes are needed before they are made. The author begins his proof on why new headings are needed by providing a partial Process FMEA that is populated with improper data. The author further complicates matters by leaving out the most important column of the Process FMEA for risk management which is the Prevention Controls column. If one wants to prove an existing Process FMEA does not work, one should show how it fails when used correctly not how it fails when used incorrectly.
When the author identifies the problems created by the “old FMEA” and provides his solution to the problems created by the improperly constructed Process FMEA, it becomes readily apparent if the original Process FMEA using the existing Process FMEA headings was properly populated with all columns shown, there would be no problems that needed to be solved with new headings the author is suggesting.
In closing, after 30 years in the field I have seen many attempts to fix what does not need to be fixed. When I see these types of misinformation, I can either not say anything or attempt to educate the people who want to experience the true powers of FMEAs on how the existing FMEAs in their current form can be used effectively. Since I want to see people experience the true powers of FMEAs I will always take exception to public documents that can negatively influence the people I want to help. Unfortunately, some people can be offended because of the responses.
I find the author’s apology to my initial response amusing. As someone who has written many technical papers that contain information that some people disagree with, I welcome challenges to information I am presenting. The answering of the challenges gives me a second opportunity to educate. I would love to see the author explain how any changes to the Process FMEA headers are needed when the Process FMEA is performed as described in my response and not as described in the paper.
One final comment. Since the introduction of ISO 9001:2015 there have been numerous articles on how the existing FMEAs must be changed to be compliant with the standard. This is simply not true. If you are performing the various FMEA types correctly and they are properly integrated within your Product and Process Development System, you will have the backbone of a system which complies with all the "Risk Based Thinking" requirements of the ISO standard.
Thank you again Richard for
Thank you again Richard for your comment. I stand by my comments and the article when I say FROM MY EXPERIENCE, renaming the column headings have helped 100% of the suppliers I have worked with. Your experiences may be totally different. I too have been working with FMEA’s for many years and it is surprising to see how they have fallen to the waste side (again, from my experiences only). Seems we have a new opportunity to bring them back to the forefront with the requirements of ISO:9001:2015. Hopefully your approach may help some people use it appropriately as well. Again, from my prospective the approach I described in the article has already proven to help and is working much better than what they were doing before. You too should expect comments from post you make, especially when they attack the “author” and not the content. When you open with such negative statements to instantly try and discredit the author you are opening the door to some feedback of your own. I think you had some great points in your comment and some that I would love to talk about further. Sounds like you have the technical aspects of the FMEA down, your delivery though…..
Intent Of Response
Contrary to what you might believe, the initial response was not intended to attack the author. Rather than stating 'The Author states" I could have used a more politically correct "The Article states" when referring to the paper. Maybe I just have thick skin after all the years I have been in the auto industry but I would not take offense if someone responded to an article that I have written and did so by beginning with the words "The Author states" since I was the one who wrote the article. Since my knowledge of you is limited to the article you created, I am in no position to judge you. It is also important to state that I would never attempt to discredit an individual in a public forum regardless of how much I knew about them. If you believe I was attacking you personnaly, please accept my apology for that was not my intent.
My response was intended to show the weaknesses of the heading changes the article proposed which I believe would have significant negative consequences on the plant which I ran and the many companies I have worked with over the past 30 years. One topic that I should have talked about in the response is the negative impact the heading changes you are proposing would have on the ability to link the Process FMEA to the Design FMEA and Process Control Plan which must be done. It is critical that all core tools of a risk management process be properly linked which your propsed methodology prevents in some instances. These linkages allow the company to perform many day to day activities that significantly reduce risk exposure in a very efficient way.
We are obviously both passionate about FMEAs and their potential. I do not doubt that you have helped companies. I just believe there are methods that could take them even further.
Add new comment