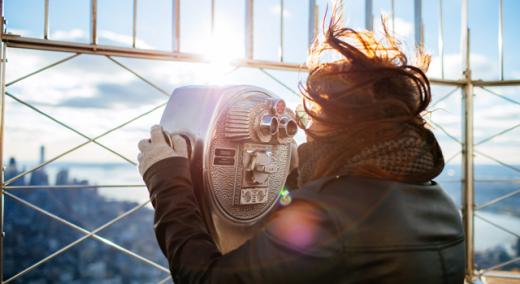
The ability to observe relationships, patterns, and environment may be deemed a “soft” skill, but there’s plenty of hard data supporting the power of observation in the workplace. After all, observation is the sometimes overlooked first step in the scientific method: Make an observation, and from there you can ask a question, form a hypothesis, and close in on a solution.
ADVERTISEMENT |
Observant people produce quality work—by catching their own mistakes
From planning to implementation, people who are deemed good observers also produce high-quality work. They have the skills to ask the right questions and notice important details—resulting in less waste, whether that’s time, money, excess production, or other valuable company resources.
In college, I worked at the Writing Center at Highline Community College. The Writing Center was part of the larger tutoring center, and students could sign up for 25- or 50-minute sessions. During those appointments, we would read over their assignment guidelines and then delve into reading their paper. We’d take notes, discuss what we noticed, and ask them questions when there was need for clarification.
…
Add new comment