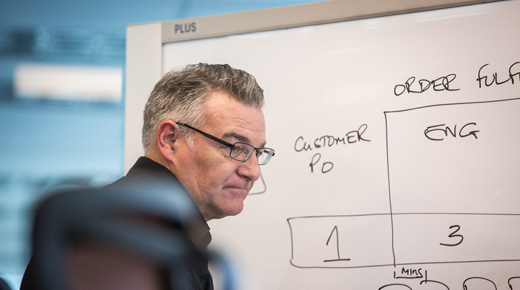
As manufacturing finds its way through the 21st century, there’s a groundswell change emerging. Organizations are jockeying for competitive position as they endeavor to describe this phenomenon. Industry 4.0, the fourth industrial revolution, and the industrial internet of things (IIoT) are a few terms being tried on for size. Although the current transition is enabled by technology, there is a timeless underlying impetus: productivity.
ADVERTISEMENT |
The first industrial revolution involved physically mechanized production—machines powered by water, steam, or internal combustion engines. The second used electric power to create mass production. The third used electronics and information technology to automate production. Now a fourth industrial revolution is building, characterized by a fusion of technologies enabling real-time data to be collated, analyzed, and actionized right in the production environment.
Early industrial revolution mainly focused on increased output. For a while, those brute-force methods were advantages, and productivity flourished. But as improved transportation and communication shrunk our world, global competition revealed the bloated underbelly of inefficient mass-production methods.
…
Add new comment