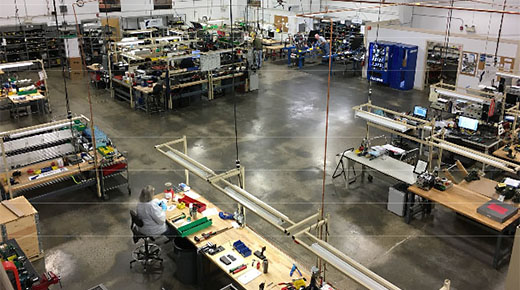
American Rheinmetall Systems (ARS) LLC, formerly Vingtech, is located in Biddeford, Maine. Established in January 2007, as part of a Norwegian company that had received a supplier contract for the U.S. Army’s CROWS remote weapon station program, the company was acquired by the Rheinmetall Group in June 2010. In 2016, the company changed its name to American Rheinmetall Systems to better associate itself with its parent company in Germany, Rheinmetall Defence.
ADVERTISEMENT |
ARS is a mechanical and electro-optical engineering company specializing in sophisticated system integration, assembly, and R&D. Its core business has not changed over the years; ARS still supports the remote weapon station but has also won additional contracts with the U.S. Army and Navy. Electro-optics and fire controls are their specialties; assembly and testing is done at their plant in Biddeford.
They don’t do fabrication; all the components are purchased from suppliers. These are militarized products that must perform in rigorous environments, in both high and low temperatures, and through heavy vibration. The tolerances to make them work across this wide band are incredibly tight; everything has to go together exactly.
…
Add new comment