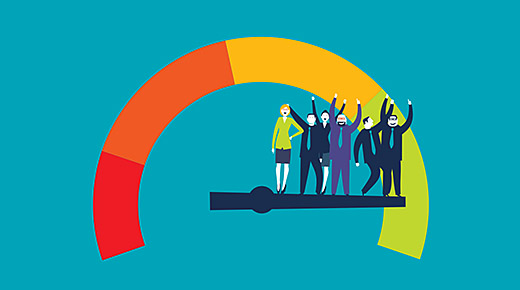
As the global economy grows, it’s more necessary than ever to stay on top of efficiency. Keep up with increasing production demands by implementing a continuous improvement method to streamline the workflow.
ADVERTISEMENT |
Continuous improvement is an ongoing effort to improve products, services, and processes. It starts with small, incremental changes, and over time it adds up to produce major improvements to productivity, quality, and cost savings. A 5S system is an effective improvement tool to guide this process.
5S—A method of improvement
5S is a Japanese management approach originally developed by Toyota as part of its lean manufacturing system. It helps correct inefficiencies and ensure smooth operations by keeping the workplace clean, functional, and orderly. It’s also designed to support a workplace culture of continuous improvement. 5S is one of the easiest ways to build a foundation for operational success because it consists of simple planning, and it can be implemented quickly in every aspect of a business.
…
Add new comment