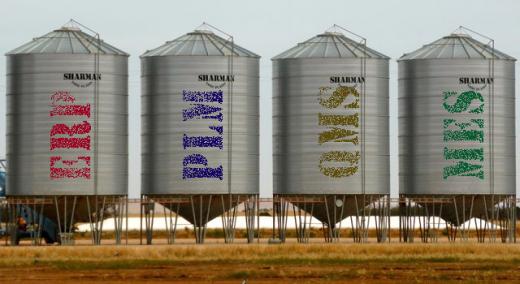
Today’s manufacturers have plenty of software solution options that are meant to enhance their productivity. You may be familiar with each of these software packages. However, if you are not, it is important to understand what each of these software packages are designed to deliver.
ADVERTISEMENT |
Enterprise resource planning (ERP): ERP systems help you to focus on the business aspects of your manufacturing processes. This includes things like supply and demand, scheduling, actual costs, accounting, and more. In essence, ERP tracks the execution of the business aspects of manufacturing. But while an ERP system offers high-level tracking of many business operations, it may have gaps in specific functionality. These gaps are often filled by additional software like PLM, MES, or QMS.
Production life-cycle management (PLM): The PLM system was developed to help track processes and product innovation. As such, it focuses on design, development, and production planning. In other words, PLM focuses on the innovation of your product line.
…
Comments
Integration
Thanks Wendy,
A useful article. You are absolutely correct that each package (ERP, PLM, QMS, MES) have a purpose and some of the vendor's solutions are great at doing it. Each system tends to be its own master data holder and rarely share their valuable information. Integration of data should be easier than it is. There are several reasons why it rarely happens. There is rarely a person that understands the details of multiple systems well enough. The developers or integrators tend to be selfish, their first reaction is typically we can do that, and rarely consider what is the best solution. One of many examples of integration gone wrong is a very recent SAP rollout. The SAP integrators best offer was to generate an overnight CSV file holding production run data for the operators. With multiple production changes currently occurring hourly (which is an issue), they were offering an unusable solution. We wanted the latest information in realtime from the new system so that we could continue to automatically verify actual material was valid at the point of selection. Effectively they are going backwards, and are asking operators to bypass the system and they will end up with bad data. The answer we get is along the lines of let's see how it goes, they are the experts and know best, I am sure they have considered the consequences of that.
The lines between the various systems are often too strong, there is a lot of shared information. MES systems tend to be the best at sharing data, but I may be saying that because they are the systems I have been involved with most.
Integration is hard work but well worth the effort of getting it right. understanding the data, where it is best used, held and sourced is a key.
Add new comment