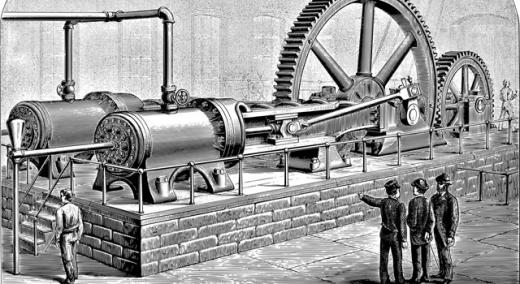
Industrial engineers design, develop, test, and evaluate integrated systems for managing industrial production processes. Functions include quality control, human work factors, inventory control, logistics and material flow, cost analysis, and production coordination. These and other facets are usually part of the job description when being hired.
Although the Bureau of Labor Statistics estimates a 10-percent growth rate among industrial engineers from 2019 to 2029, the attrition rate is anecdotally just as high; that equates to 100-percent attrition in a decade. Nowhere is the dissatisfaction and attrition of industrial engineers as great as in the engineer-to-order manufacturing space.
…
Add new comment