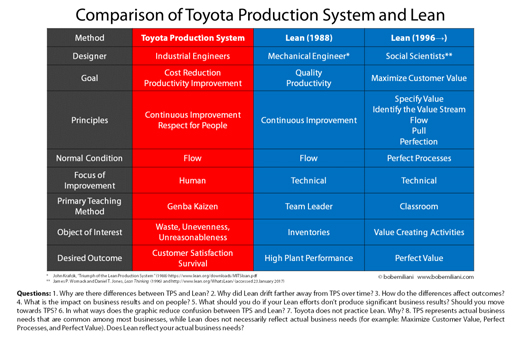
I recently posted a version of the graphic below with the caption: “Not perfect, but close. It’s about right.” The response was overwhelmingly positive. A great majority of people recognized it as a unique comparison, one that they had never seen before, and also as an accurate comparison that effectively captures differences that actually exist.
ADVERTISEMENT |
My intent in producing the graphic was to address the decades-long confusion that has existed between the Toyota Production System (TPS) and lean, and to help people understand the critical differences. It was also to help people realize why they are often unable to achieve much success with lean despite a lot of effort over many years.
…
Add new comment