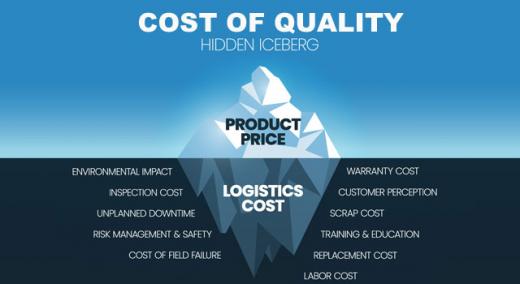
Manufacturers spend too much on quality issues. Some issues they are blind to, some are due to poor detection, and some are the costs incurred when issues escape to a customer.
ADVERTISEMENT |
It seems like in recent years the challenges have been great in both magnitude and quantity—supply chain turmoil, global unrest, and workforce challenges are just a few examples. To confound things, issues seem to be circular in nature, one influencing the other. This puts immense pressure on the margins of manufacturing organizations. There has to be a way out... and it starts with changing the way we think. The Roman emperor Marcus Aurelius once said, “The happiness of your life depends upon the quality of your thoughts.”
I claim there is money to be had in how we approach manufacturing. During the past few decades, manufacturing has made significant strides in the consistency and quality of products, but at what cost? This is an elusive question. Of the hundreds of customers I’ve worked with over the past couple decades, few really know the true costs.
…
Add new comment