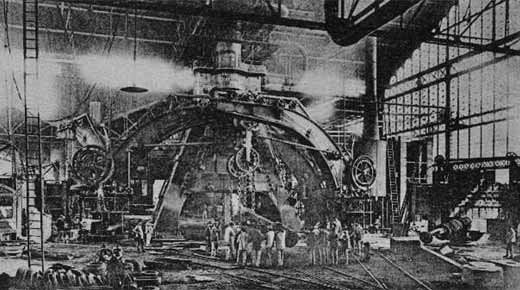
Imagine a factory with a large monument machine. It takes several days to set up. When it does run, it runs very fast, much faster than you can actually use its output. Therefore, you take the excess output and store it to use later. Actually, you don’t know how many items you need to make, so you make as many as you can while the machine is available to you.
ADVERTISEMENT |
Some of that excess output may prove to be less useful than you thought, but there is pressure to use it all anyway since it was so expensive to produce.
After a run making items for one process, you change it over to make items for a different process, and build up a queue of output there.
When all of the output is used, it all may or may not work the way you expected it to.
Most of us would see this as a classic case of “overproduction”—overwhelming the system with excess output that hasn’t been checked for quality, that isn’t needed right now, and might or might not be useful in the future. But it seemed like good efficiency to make it while we could.
…
Comments
Making improvements vs. teaching how to make improvements
I think a more important question that your article hinted at but did not articulate would be:
"Is it because we have not empowered them to make the necessary improvements even though they have the requisite knowledge and experience to do so?"
Add new comment