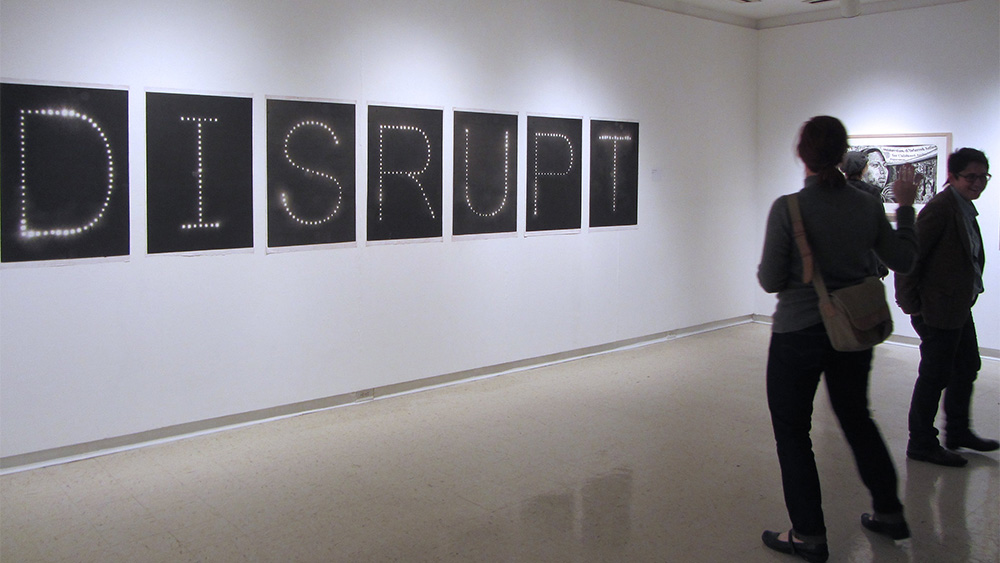
badsci/Flickr
Body
Lean supply chains are designed based on several key principles. First, the general philosophy of lean is to reduce or eliminate nonvalue-added waste. The concept of reducing waste is always beneficial to organizations. We should continuously strive to reduce things like wasted time, wasted effort, wasted processing, wasted travel, and wasted packaging. So, even in times of disruption or crisis, efforts to reduce wasted steps or processing can actually benefit the organization. This efficiency is a good thing.
…
Want to continue?
Log in or create a FREE account.
By logging in you agree to receive communication from Quality Digest.
Privacy Policy.
Add new comment