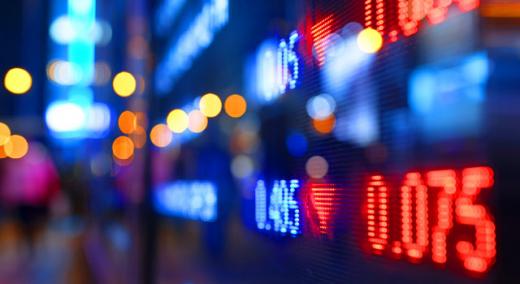
Quality managers have a problem. The success of their quality program hinges on one thing. It’s not KPIs, and it’s not methodology. It isn’t even employee engagement or customer satisfaction. The one thing a quality manager needs most is leadership buy-in.
ADVERTISEMENT |
Quality programs fail because they do not have support from the top.
So how can you win executive support? Run a quality program that gets results. Results like increased customer satisfaction, employee engagement, and more efficient processes reflected in the bottom line. Improved profits tied to your quality program will get the attention of your executive team, guaranteed.
…
Add new comment