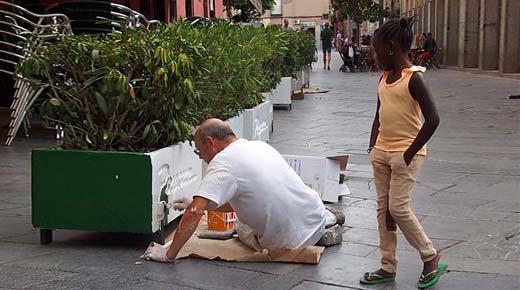
A few spare moments can be turned into an opportunity to observe processes to find waste.
Credit: Luis Triguez
Many of us are familiar with the concept of the Ohno Circle, innovated by Taiichi Ohno at Toyota during the 1940s. While familiarity with the technique and the goals it sets to accomplish is one thing, how many of us have actually participated? The surprising answer is… probably all of us, in a way.
ADVERTISEMENT |
During the 1940s, Ohno established the famous Toyota Production System, and with it one of his most famous exercises, the Ohno Circle. Employees are tasked with standing inside a circle (either drawn with chalk or simply imagined) for hours and simply observing the processes until they find waste. From there, they seek to eliminate it. For a more in-depth overview and examination, check out this recent QD article by Bonnie Stone, A New Spin on the Ohno Circle.
While his exercise remains extremely well known, how many can say they confined themselves to one location for an extended amount of time and just watched? Some of us might say no, but I’m positive most of us have stood (or sat) in place for upwards of at least an hour (but less is OK!) at someone else’s business.
…
Comments
Great concept!
Nearing the end of our Lean training we would send participants to lunch in a food court environment to observe 2 pre-selected outlets (with and without attention to Waste), obtain some performance data at distance and study what in their operations accounted for the difference. A great live learning experience!!
Involve the customer in identifying waste
Add new comment