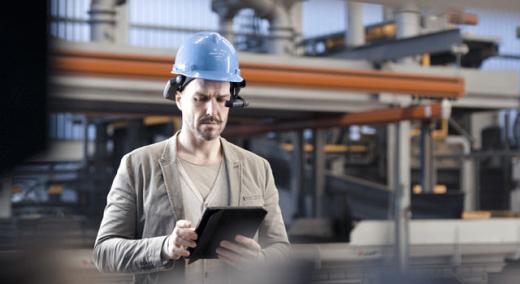
Solving problems goes beyond noticing the symptoms and wanting to resolve them. It’s also necessary to perform a root cause analysis, pinpointing the factors likely to have made an issue occur. It’s only then that leaders can create concrete solutions for lasting changes. However, root cause analyses can be extremely time-consuming. Fortunately, artificial intelligence (AI) can provide high-speed data processing capabilities that make these investigations more efficient.
ADVERTISEMENT |
Receiving the knowledge to cope with unwanted circumstances
When modern manufacturers see sales trends going in the wrong direction, they must act fast to determine why. Is the issue due to a short-term matter, or is the consumer disinterest a result of a prolonged problem?
AI works well for cutting through all the data noise that could lead humans to the wrong conclusions. It can also reduce information-preparation errors that make the findings incorrect or less useful. Consider the case of USAopoly, a game and puzzle manufacturer: The company dug into data to determine root causes, but it took a prohibitively long time.
…
Add new comment