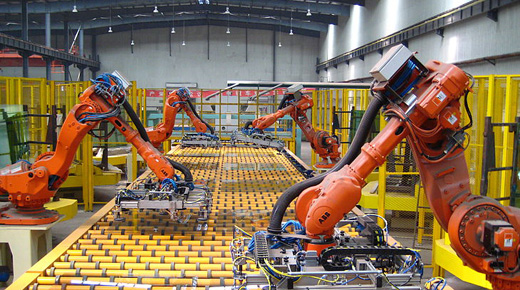
The fourth industrial revolution is upon us. Collecting real-time production data is becoming more common as enterprise-wide software develops into a tool that enables transformative gains in productivity. Although not common, there are “lights-out” factories, such as the fully automated FANUC manufacturing facilities, in operation today. And AI has become a ubiquitous plug-in for nearly every sector imaginable. “Industry 4.0” and “smart manufacturing” are now familiar terms in the manufacturing lexicon. The caveat to the fanfare is the same as with the first industrial revolution: “What is the future of humans in all this?”
ADVERTISEMENT |
Man vs. robot misconception
Although automation is only one aspect of Industry 4.0, it seems to receive an inordinate share of digital ink, second only to AI. The nugget of concern seems to be fear of robots and full automation replacing human employees in manufacturing. Considering that the debate over the effect of current levels of automation on levels of unemployment still rages, perhaps it’s a concern worth examining.
…
Add new comment