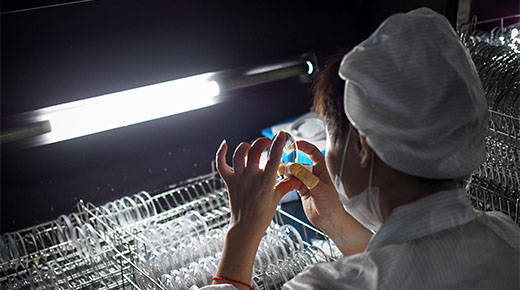
It seems to happen to every company, big or small, newcomer or seasoned expert. You ship a product design off to a manufacturer, and something goes wrong on the manufacturer’s side. The problem crops up in the design, production, or packaging, and leads to a bad apple in a batch of otherwise great products, or worse, a batch of unshippable product.
ADVERTISEMENT |
One of our friends, who oversees quality and product at an innovative eyewear startup in San Francisco, posed this very problem to us at Valkri Intelligence, where we develop deep-learning solutions for better quality control. We broke the problem down into three main points:
• How can we eliminate delays due to flawed optical products and guarantee near-perfect product quality?
• How can we provide insight into the quality control process?
• How can we achieve this through technology?
Let’s look at some of the ways you can integrate technology into your quality control process to address similar issues and achieve your quality, supply chain, and product goals.
…
Add new comment