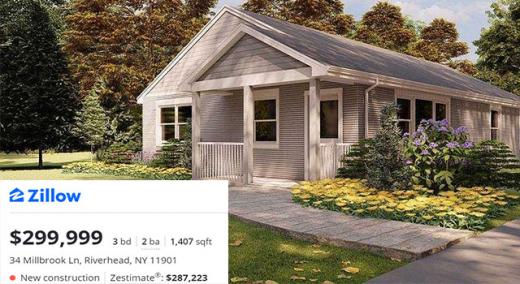
‘For sale: 3 bd, 2 ba, 1,407 sq ft home in Riverhead, NY,” the groundbreaking listing on Zillow reads. “Own a piece of history! This is the world’s first 3D-printed home for sale [on the open market]. The future begins with this historic property!” Perhaps the exclamation marks are warranted.
ADVERTISEMENT |
Printed by New York-based SQ4D using its patent-pending ARCS technology, this home was architecturally designed by nationally renowned engineering firm H2M, which took care to incorporate efficiency codes and lower energy costs. SQ4D claims its process provides a stronger build than traditional concrete structures while using a more sustainable building process. With complete confidence in the quality of its product, SQ4D will be including a 50-year limited warranty on its 3D-printed structures.
…
Add new comment