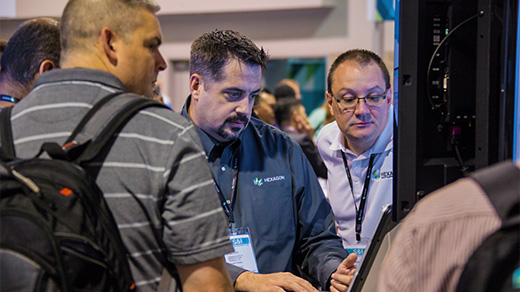
If there was one key takeaway from Hexagon’s impressive and impressively large user conference, styled “HxGN Live,” which took place earlier this month, it’s that finding actionable information, not merely acquiring mountains of data, is the key to developing a truly smart factory. “It’s always about information, never about data,” Hexagon CEO Ola Rollen confirmed during his opening keynote at the show.
ADVERTISEMENT |
Context is the most important factor necessary to unlock information from data, and the human brain teases out context exquisitely well. Machines, not so much—yet. In areas as diverse as autonomous driving, resource management, building, geospatial positioning, and smart manufacturing, however, Hexagon is engineering a future in which machine learning will establish feedback loops to increase efficiency and reduce response times. Rollen credits human intuition with our unique problem-solving abilities; creating a kind of digital intuition and embedding it into machine-based systems is the endgame. It’s an open question as to how long before that ambitious goal comes to reality.
…
Add new comment