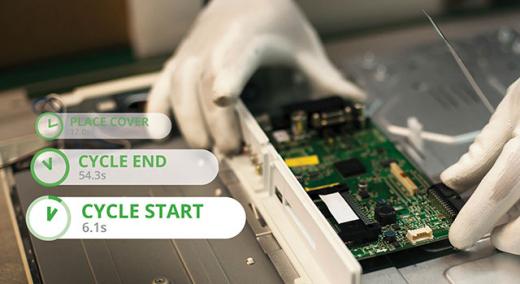
We are a full two years into post-pandemic manufacturing life, with the omicron variant the latest cause for concern. It might sound hyperbolic, but I’m pretty sure manufacturing will never be the same as it was in 2019. In some ways, that’s a good thing.
ADVERTISEMENT |
One silver lining of the novel coronavirus was the adaptability that it forced on many manufacturers. For all the disaster planning and preparedness exercises companies practice, there’s nothing like a true crisis to test the system and show the gaps in it.
But pandemics aren’t the only hurdles on the manufacturing horizon. We know that natural disasters are increasing in frequency. Supply chain disruptions and political upheaval are also growing concerns around the globe. In a recent Drishti survey, we found that 60 percent of the 400 manufacturers that responded believed a significant disruptive incident would likely occur during the next 12 months.
With that level of uncertainty plaguing the industry, the question has to be asked: How do manufacturers continue to deliver high-quality products when they’re sure to be impacted by happenings outside of their control?
…
Add new comment