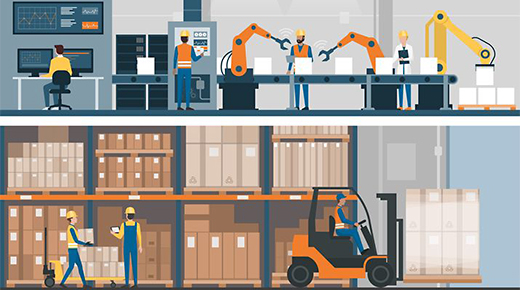
Technological innovations on all fronts are evolving quickly and are developed, manufactured, and sold worldwide in aerospace, medical device, communications, automotive, and many other industry segments. It’s hard to keep up with these breakthroughs because they are growing exponentially. But despite all the technological innovations, one critical issue has persisted since the first industrial revolution during the mid-1800s: the engineering, manufacturing, and quality “interpretation” by companies’ suppliers, whether internal or external.
ADVERTISEMENT |
For many years geometric dimensioning and tolerancing (GD&T) has been the engineering, manufacturing, and quality processes language. The origin of GD&T has been credited to Stanley Parker, who worked at the Royal Torpedo Factory in Alexandria, Scotland. Parker started to develop the concept in 1938, and for nearly 20 years he added more into the language, culminating in his last book, Drawings and Dimensions (Pitman, 1956).
…
Comments
GD&T Dictionary - Automated or Otherwise
Unfortunately a common language is of very little use to illiterates. Too many engineers today cannot communicate in complete sentences - either verbally or in writing, let alone speak a common technical language. Several years ago, a licensed PE working for Federal Highways demanded that my office enforce exact placement of concrete reinforcement based on their measurement of elements in a drawing that was clearly marked "Not to Scale" and where the only dimension given was a minimum depth of cover.
When a second PE working for my agency concurred with the Fed's determination, I inquired about tolerances for deviation. I was told that we were to accept "zero" tolerance. I inquired futher as to what was meant by zero. The engineer looked at me quizzically and asked what did I mean. I explained about standard tolerances and said that we needed to define zero in terms of the number of significant digits we wanted to use to define the tolerance. The engineer got very red in the face, slammed their fists onto the conference table and screamed that "zero meant zero". So we interpreted that to mean that they wanted 0" giving us a standard tolerance of +/- 0.5" where the previous defined tolerance for these units was .25" -going to show that you get what you pay for all around.
Add new comment