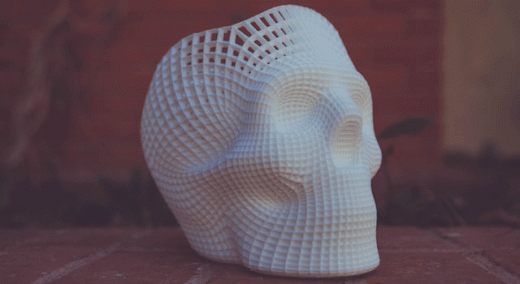
Simulation is a necessity for automotive companies in the 21st century, and there’s pressure to use more of it for many reasons: 1) Electrification produces more heat sources that need CFD and thermal analysis to design dissipation strategies; 2) industrywide moves toward minimal or “zero” prototype builds make crashworthiness and structural simulation more important; 3) advanced driver automation systems (ADAS) and autonomous vehicles require constant data collection and processing via simulation; and 4) smart connected systems in a car have increased the number of chips and the need for electronic system design (ESD) and simulation.
ADVERTISEMENT |
The engineers at VI-Grade are especially keen to move the industry toward zero prototypes. The German simulation and driving simulator company even has a yearly event called the ZERO PROTOTYPES Summit. To help bring this future to fruition, earlier this quarter VI-Grade announced AutoHawk for the North American market, a hardware-in-the-loop (HiL) simulation platform. The company hopes the tool will reduce prototypes because the simulators are highly configurable and can therefore meet the validation needs of internal combustion engines, electric vehicles, and many other customer and consumer use cases.
…
Add new comment