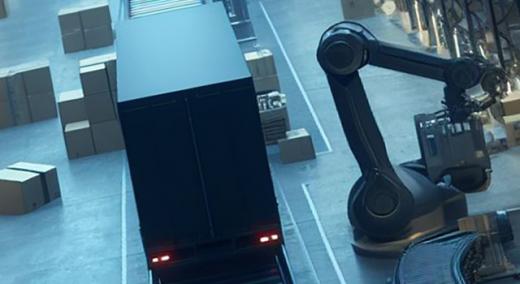
As the growth in fulfillment warehouses, e-commerce, and third-party logistics skyrockets, and unique customer demands evolve, more companies are exploring the concept of dark warehouses—fully automated, “lights-out” facilities that use intelligent, interconnected devices to operate without human labor. Due to labor availability, cost-benefit analysis, technological advancements, and other factors, the shift toward these facilities continues.
ADVERTISEMENT |
Dark warehouse drivers
Although the reasons for advanced technology integration, including robotic automation, will vary from one enterprise to another, there are multiple key concepts and innovations prompting the gradual move toward “darker” warehouses.
Refined robotic tools
More affordable, robust, and energy-efficient robots can now be easily integrated into a wider variety of operations for increased capacity. Intelligent peripherals—including sophisticated vision, sensor technology, and flexible end-of-arm tooling (EOAT)—all work together to facilitate fluid product flow with improved quality.
…
Add new comment