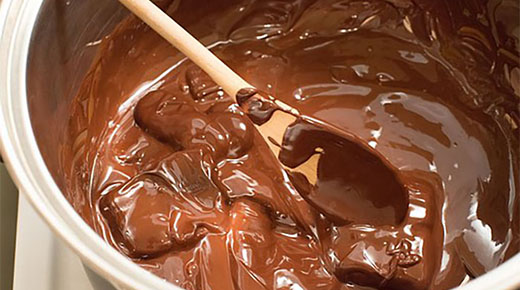
Contrary to that old cooking adage, “a watched pot never boils,” keeping a careful eye on things—in the kitchen or in the laboratory—can be essential to making a useable (or edible) final product.
ADVERTISEMENT |
Take chocolate, for instance, that foundational block of the food pyramid. An important part of creating high-grade chocolate is a step called “tempering,” or the melting, stirring, and cooling of the liquid chocolate to align the crystals that give it a smooth texture and a glossy shine. One of the key senses chocolatiers use to monitor tempering is sight, giving them information on the thickness and color of the batch to make sure it tempers evenly as it cools.
But what if they had to do it blind?
For many years, that’s exactly what has been happening in metallurgy laboratories across the world. While the crafting of specialty metal alloys, like titanium or zirconium, can be far more complex than making chocolate, metals are often put through a process that is somewhat akin to chocolate tempering—vacuum arc remelting. Vacuum arc remelting is an important step in metal fabrication, the process by which the chemical and physical homogeneity of the material is refined to ensure a quality end-product.
…
Add new comment