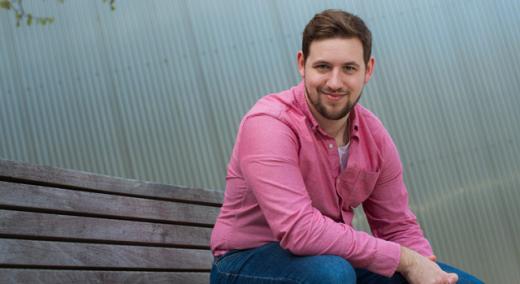
When Alexander O’Brien sent in his application for graduate school at MIT’s Department of Nuclear Science and Engineering, he had a germ of a research idea already brewing. So when he received a phone call from Professor Mingda Li, he shared it: The student from Arkansas wanted to explore the design of materials that could hold nuclear reactors together.
ADVERTISEMENT |
Li listened patiently and then said, “I think you’d be a really good fit for Professor Ju Li,” O’Brien remembers. Ju Li, the Battelle Energy Alliance Professor in Nuclear Engineering, had wanted to explore 3D printing for nuclear reactors, and O’Brien seemed like the right candidate. “At that moment I decided to go to MIT if they accepted me,” O’Brien remembers.
And they did.
“After years of knowing I wanted to work in green energy but not knowing what that looked like, I very quickly fell in love with [nuclear engineering],” says MIT Ph.D. student Alexander O’Brien. Photo: Gretchen Ertl.
…
Add new comment