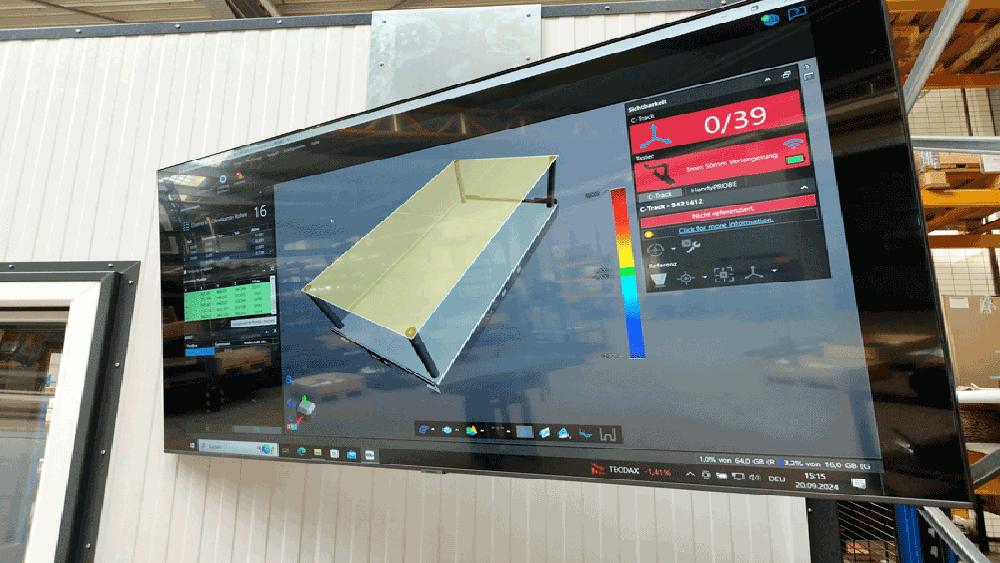
Creaform
The built-in Creaform OS 3D scanning software provides real-time visualization of components that have been captured.
Brosius GmbH is a trusted partner in metal processing for a wide range of companies in the mechanical and plant engineering industries, offering comprehensive services under one roof. Brosius ensures that every part it manufactures in its 10,000 m² state-of-the-art production hall meets or exceeds customer expectations.
ADVERTISEMENT |
Fabian Otto, a certified mechanical engineer, designer, and technical project manager at Brosius says, “Quality is our No. 1 priority. Our controlled process management system ensures that we manufacture components that meet the highest standards.
“Our planning and design department manages every aspect of customer orders, including initial planning, development, advanced 3D design, prototyping, series production, and comprehensive project documentation. This holistic approach means that we can efficiently prepare and finalize all projects, ensuring exceptional results every time.”
…
Add new comment