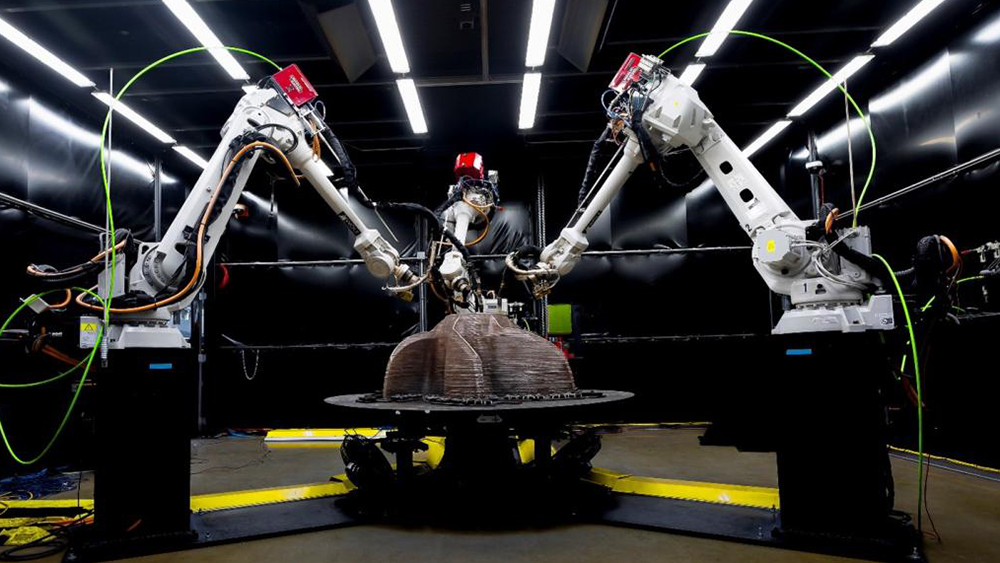
This PM-HIP can was printed on the Oak Ridge National Laboratory’s MedUSA wire-arc additive manufacturing machine. The can will be used to create an impeller for a hydropower impeller to demonstrate a new approach for creating large-scale clean energy components. Credit: Carlos Jones/ORNL, U.S. Department of Energy
Researchers at the U.S. Department of Energy’s Oak Ridge National Laboratory are using advanced manufacturing techniques to revitalize the domestic production of very large metal parts that weigh at least 10,000 lb each and are necessary for a variety of industries, including clean energy.
ADVERTISEMENT |
Across sectors spanning aerospace, defense, nuclear, oil, gas, renewables, and construction, sourcing these large-scale components is an increasingly urgent challenge. This need is felt acutely in the U.S., where traditional manufacturing techniques like casting and forging have declined and moved overseas—resulting in supply-chain shortages.
Today, ORNL researchers are advancing an increasingly viable alternative to casting and forging known as powder metallurgy-hot isostatic pressing, or PM-HIP. Their research has the potential to bring large-component manufacturing back to the U.S.
…
Add new comment