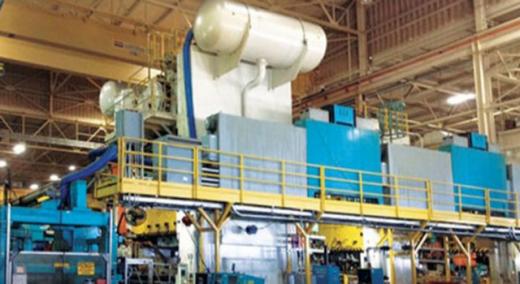
Courtesy of MetalForming magazine
In metal stamping, especially in critical automotive applications, sometimes it’s not enough simply to close the control loop. Traditional control algorithms rely on eliminating an error between what is happening—as indicated by feedback from system sensors—and what should happen. High-speed motion controllers quickly perform such tasks.
ADVERTISEMENT |
But what if, for product-quality reasons, no striking errors must occur in the first place? For example, what if the risk of making an impression too quickly or too heavily when stamping an automotive part must be avoided? Slowing the press might work, but doing so reduces productivity.
|
…
Add new comment