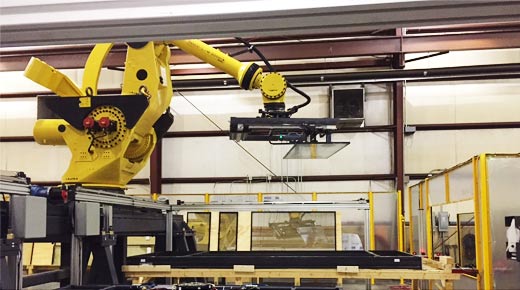
Sponsored Content
Opportunities are becoming more frequent to apply metrology to adaptive robot control for many applications. There are many different techniques to accomplish this, from regular calibration to real-time feedback, using anything from laser trackers to optical devices in order to capture high-accuracy position data for these processes. ATT Metrology recently provided automation to complete an adaptive robot control (ARC) system designed to install large glass panes into custom window frames.
ADVERTISEMENT |
The system integrated a laser tracker into a robotic build process that utilized a large industrial robotic arm. Robotic arms are known for their repeatability, but accuracy in high precision is difficult to achieve without an outside system to guide the robot’s end effector to known positions. To achieve better accuracy, we created a system that measured corner cube targets on the end effector to obtain a location frame at key positions in the process, then provided a frame-to-frame transformation from the robot’s reported position to the measured one. This allowed the robot to make fine adjustments in the end effector position to coincide with the target location.
…
Add new comment