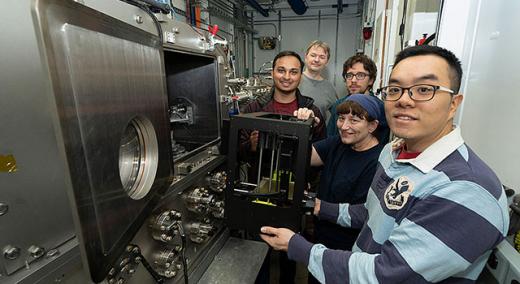
A team of scientists working at the National Synchrotron Light Source II (NSLS-II) at the U.S. Department of Energy’s (DOE’s) Brookhaven National Laboratory has designed an apparatus that can take simultaneous temperature and X-ray scattering measurements of a 3D printing process in real time, and has used it to gather information that may improve finished 3D products made from a large variety of plastics. This study could broaden the scope of the printing process in the manufacturing industry and is also an important step forward for Brookhaven Lab and Stony Brook University’s collaborative advanced manufacturing program.
ADVERTISEMENT |
The researchers were studying a 3D printing method called fused filament fabrication, now better known as material extrusion. In material extrusion, filaments of a thermoplastic—a polymer that softens when heated and hardens when cooled—are melted and deposited in many thin layers to build a finished structure. This approach is often called “additive” manufacturing because the layers add up to produce the final product.
…
Add new comment