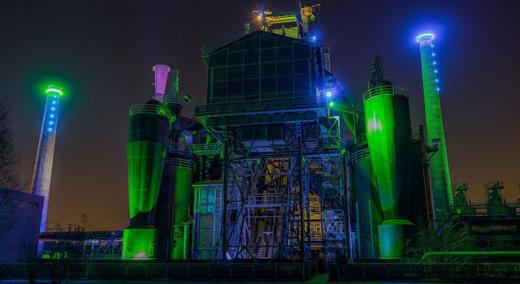
Manufacturing is stepping up investment as the U.S. economy recovers from the challenges of 2020. Nearly 40 percent of manufacturers have increased CapEx spending, with less than 7 percent planning to spend less, the National Association of Manufacturers reports.
ADVERTISEMENT |
With that investment, factories have substantial room to reduce waste and improve profitability. In many plants the key efficiency metric, overall equipment effectiveness (OEE), stands at just 60 percent—meaning 40 percent of potential production capability is lost. In contrast, state-of-the-art factories regularly achieve 85 percent OEE.
Getting to real-time insight
Digital tools can be an important lever to help factories and entire manufacturing ecosystems dramatically reduce waste. As a foundation, most digital technologies start by providing real-time insight into what’s going on, what’s going wrong, and why. With that information, operators can act more quickly to fix issues as they occur and even prevent problems.
…
Add new comment