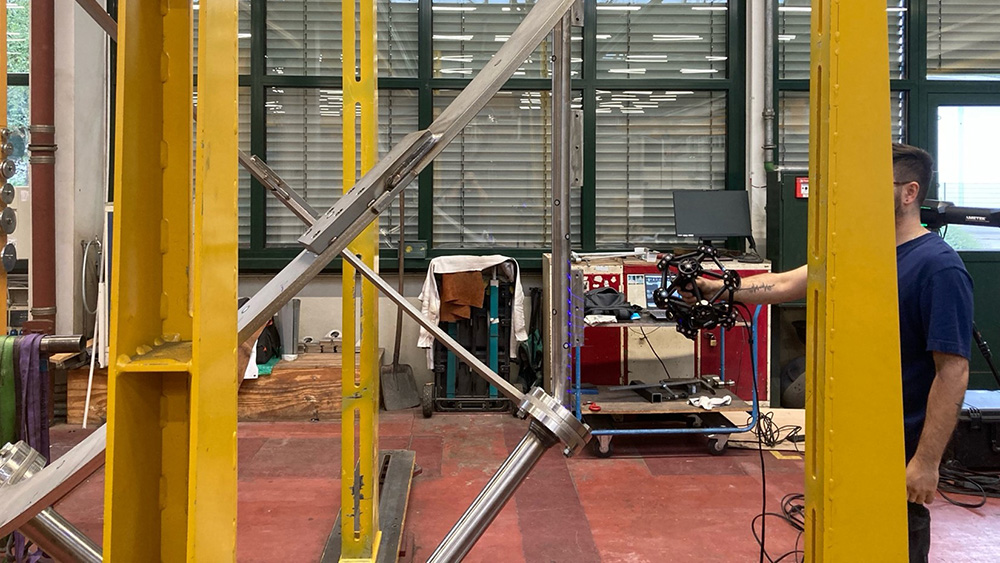
Creaform
Thanks to its design and accuracy levels, the MetraSCAN BLACK+|Elite 3D scanner can be used to acquire reliable and repeatable 3D measurements—right on the production floor.
For more than 90 years, EKATO Rühr- und Mischtechnik GmbH has specialized in process analysis, engineering, scale-up manufacturing, and assembly of agitator technologies, continually developing solutions to meet the needs of process-oriented industries. Supporting procedures such as homogenizing, dispersing, and heat transfer, EKATO agitating systems are recognized for their reliability, durability, and exceptional quality.
ADVERTISEMENT |
With more than 560 employees and 60 offices worldwide, EKATO has delivered more than 250,000 agitators, helping businesses achieve outstanding new levels of operational performance.
The challenge: Ensure top quality control of complex, large-scale components
Over the years, the EKATO engineering and quality control teams noticed customers placed higher demands on its agitator systems. The design and configuration of the agitating systems, along with the selection and arrangement of individual components, play a crucial role in improving their mechanical efficiency as well as those of the reactors and their internal structures.
…
Add new comment