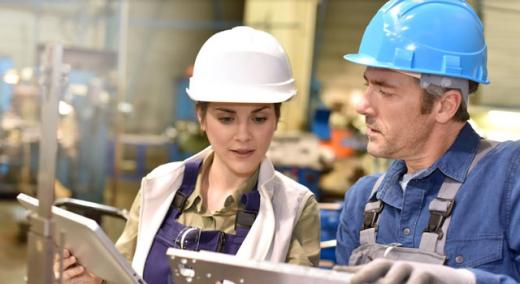
Twenty years ago, digital tools were “a thing.” Now they flow through all things.
ADVERTISEMENT |
To some degree, every manufacturer is now a digital company. And with the right modern platform, any manufacturing organization can break down silos of ownership to focus on the intersection of people, processes, and technology. Here at Dozuki, our job is to help companies hold themselves to higher standards. Below, I’ll show you how to choose the right tools to suit your unique needs. You’ll learn how to navigate the balancing act between new technology and cultivating the people-centric processes that make businesses successful.
1. Standardization 4.0
In traditional manufacturing environments, standards are manually recorded and updated using either paper binders or clunky spreadsheets and PowerPoint presentations. By using digital tools, standards can be effortlessly and continually shared and updated.
In addition to free-flowing information, this new wave of standardization in Industry 4.0 allows for more precise control over revisions and information access.
…
Add new comment