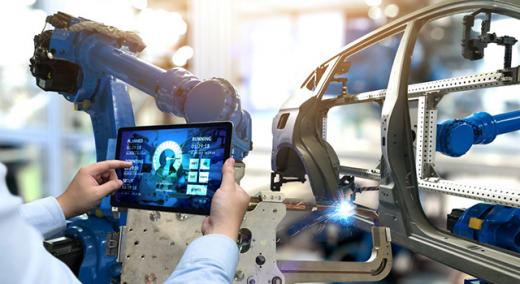
Adobe Stock
Digital applications in manufacturing are not only becoming increasingly accepted; they are expected. However, for smaller manufacturers, the process of making this switch can be daunting. Initial expenses, as well as the cost of training employees, is enough to stop the process altogether.
ADVERTISEMENT |
But beginning the process of “going digital” doesn’t have to be overwhelming. With a little guidance and education, all manufacturers can start to implement digital manufacturing concepts in a staged approach that best fits their individual work environments. Here are our top five recommendations for digital applications that can help you get started.
![]() |
…
Add new comment