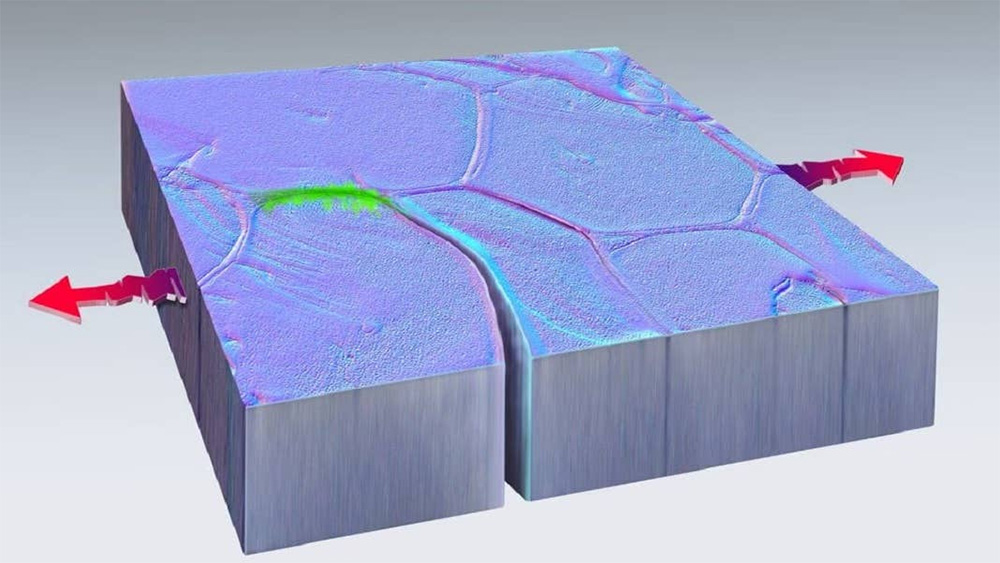
If you’ve seen the Terminator movies, you may remember the shape-shifting humanoid robot T-1000. Made of liquid metal, it could instantly self-heal bullet wounds and other injuries, its metal simply oozing back together and making any damage disappear. Decades after the concept of self-healing metal showed up in a movie, it’s left the realm of pure science fiction and moved closer to reality as scientists have for the first time observed metals able to heal themselves.
ADVERTISEMENT |
In a paper published recently in Nature, a team from Sandia National Laboratories and Texas A&M University described how they were able to see the nanoscale activity of platinum and copper using an electron microscope.
…
Comments
Self Healing Metals
I'm not quite convinced self healing is the right term to be utilized as the state of stress the material was placed under to cause cracking is coincidentally the very same stress which cause the two surfaces to vibrate upon each other at the crack boundary and fuse or as you mentioned "cold weld" the fatigue cracks back together. Had that stress rate of 300 times per second been reduced to say 60 times per second or none at all this cold weld process would not take place. I don't mean to be the downer or nay sayer. I just want science to remain as such "Science" and not news headlines that capture the eye. Self Healing! Ooohh awwww! Cold fusion welding through high cycle vibration, well nothing as WoW factor in those standard terms used in everyday manufacturing.
Add new comment